shank shank inspection standards definitions and related presentations
1. shank tapered portion of the cone tolerance
standard tolerance of the cone , the right size shank end diameter , taper length , taper strict tolerance levels are used to limit and ensure accuracy. Precision CNC tool taper is to ensure the machine tool spindle taper shank wall closely the necessary conditions , which can effectively prevent and absorb vibration generated during cutting and resistance , which are subject to various parts of the tool cutting force uniform , so as to achieve a substantial increase in the machine spindle and the tool life , and improving the surface roughness of the workpiece purposes.
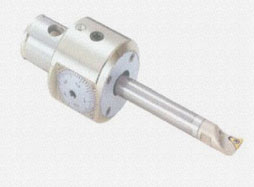
a: shank diameter d1 of the rear end to the large end of the distance, a tolerance of ± 0.2mm, can ensure the precise length of taper shank .
taper angle tolerance is divided into 12 grade tolerances, with AT1, AT2, AT3 ... AT12 representation . ATD is a unit of length expressed in microns . Indicates taper surface C and D surface diameter difference dC-dD tolerances.
can be seen from the table , the C-plane taper ( large end ) and D surface ( small end ) of the diameter of the differential dC - dD not allow the measured value is less than the given dC - dD value, and while not allowing more than dC - dD + ATD. Other words, that the cone angle of the lower deviation is zero , and the cone angle of the deviation does not allow more than ATD.
For example : For the AT3 BT40 , its dC-dD should be
17.208 ≦ dC - dD ≦ 17.208 + 0.003
Since this difference of both sides of 0.003mm, so called taper accuracy of 0.003mm, namely BT40 , in accordance with the criteria AT3 , its cone angle of taper maximum deviation of not more than 10 . "
2. Toolholder shank portion of the runout
shank Another important parameter is the test portion of the tool holder round beating. It is usually measured at the end of the toolholder .
Another expression is 3XD (5XD) at runout . The latter is closer to the cutting edge at the real runout .
well known in the machining process , especially in high speed cutting, the tool runout if too large , it will cause a series of very adverse consequences. For example, excessive tool wear , surface roughness, and may cause vibration and spindle damage and other serious consequences.
|